Exploring the advantages of a chemical-free and non-thermal solution
In the world of packaging and food safety, ensuring that packaging materials are free from microbial contamination is crucial to maintaining product quality and extending shelf life. Conventional decontamination methods rely on thermal treatments or chemical processes. However, these methods can sometimes compromise the integrity of the packaging material. An advanced and proven solution to this challenge is the pulsed light technology.
Pulsed light is a non-thermal surface treatment that has been gaining momentum in recent years due to its effectiveness in decontaminating packaging without the need for water or chemicals, or a high level of energy consumption. This method offers a promising alternative that preserves the quality of packaging materials while effectively reducing microbial load. Regularly Claranor collaborates with packaging suppliers – ie one of our collaborations with Aptar.
Discover how pulsed light technology works, its benefits, and its applications in the packaging industry.
What is Pulsed Light Technology?
Pulsed light technology involves the use of short flashes of intense, broad-spectrum light, primarily in the UV-C range, to kill microorganisms on the surface of various materials. These intense flashes of light, delivered in a fraction of a second, disrupt the DNA of bacteria, viruses, and other pathogens, rendering them inactive and preventing their replication. The process is non-thermal, meaning it does not rely on heat to achieve its antimicrobial effects. This characteristic is particularly advantageous for heat-sensitive materials that may deform or degrade when exposed to high temperatures.
How Does Pulsed Light Preserve Packaging Integrity?
One of the features of pulsed light decontamination is its ability to preserve the integrity of packaging, even for the most sensitive types. This advantage is particularly interesting in the following applications:
Caps with Liners
Traditional decontamination methods that use chemicals can lead to residues being trapped under the liners of caps. These residues can affect the overall product quality and safety. Pulsed light, on the other hand, eliminates this risk by providing a dry and residue-free decontamination process. The intense light penetrates effectively to neutralize pathogens without leaving any unwanted residues, ensuring a safer and cleaner packaging solution.
Cardboard Cups Sensitive to Humidity
Cardboard cups and containers are particularly sensitive to moisture, making them unsuitable for water-based decontamination methods. Exposure to water or humid conditions can cause these cups to warp, lose structural integrity, or even degrade. Pulsed light technology offers a moisture-free alternative that preserves the strength and shape of cardboard packaging while still providing effective microbial decontamination.
Lightweight Plastic Cups Sensitive to Heat
Lightweight plastics, often used in food and beverage packaging, can deform or melt when exposed to high temperatures. This makes thermal decontamination, as UV treatment, less viable. Pulsed light decontamination bypasses this problem entirely by using instant flashes rather than time exposure, maintaining the shape, strength, and functionality of the packaging.
Very Thin Films
Very thin films are increasingly used in packaging to reduce material usage and promote sustainability. However, these films are highly susceptible to shrinkage or distortion when exposed to heat. Pulsed light provides a gentle yet effective solution that eliminates pathogens without causing shrinkage or affecting the seal quality of the packaging. This allows manufacturers to maintain the barrier properties and overall effectiveness of the packaging material.
Benefits of Pulsed Light Technology for Packaging Decontamination
Pulsed light technology presents many benefits that make it an attractive option for packaging decontamination:
Chemical-free process: One of the most significant advantages of pulsed light is that it does not require chemicals, which can leave residues or pose environmental and health risks. This makes it a safer option for manufacturers, operators on production-lines and consumers.
No water usage: Unlike traditional methods that rely on water-based decontamination, pulsed light uses light energy alone. This not only preserves water but also reduces the risk of moisture damage to packaging materials.
Fast and efficient: The process of pulsed light decontamination is instant, taking just a fraction of a second to achieve significant microbial reduction. This efficiency can help increase throughput in production lines.
Preserve material properties: By avoiding heat and moisture, pulsed light ensures that the physical properties of packaging materials remain unchanged. This is especially important for packaging that must maintain a specific shape, strength, or barrier property.
For more information on our decontamination solution for beverages, dairy, cosmetics or for microbiological tests on your new packaging
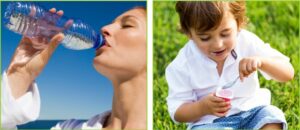