Decontamination Tunnel:
secure your production line
In production environments, hygiene and product safety are key. Manufacturers in industries such as food, beverages, and pharmaceuticals must ensure that their products are free from contamination at every stage of production. One of the most critical areas for contamination risk is during the movement of materials and packaging through different zones within the production facility. Whether it’s ingredients in large 25 kg bags, plastic bins, or other packaging materials like pillow bags, surface decontamination is essential before these items enter high-care or sterile environments. It thus avoids cross contamination.
At Claranor, we understand these challenges and have developed a decontamination tunnel. This automated, chemical-free solution offers manufacturers an efficient and sustainable way to protect their production lines from contamination while ensuring the highest level of safety and hygiene.
Why surface decontamination is critical?
Contaminants such as bacteria, viruses, molds, and yeast can easily transfer from the surface of materials into clean zones, potentially compromising the safety of the final product. This is particularly true in industries where products are sensitive to microbial contamination, such as dairy, plant-based foods, and beverages.
Traditionally, manufacturers have relied on chemical decontamination methods to mitigate this risk. However, these methods often have significant downsides, including the use of harsh chemicals, extensive water consumption, and energy-intensive processes. Moreover, chemical residues can pose risks to both the product and the environment, leading to concerns about sustainability and regulatory compliance.
This is where the Claranor decontamination tunnel comes in, offering a clean, efficient, and environmentally friendly alternative to traditional methods.
Claranor UV decontamination tunnel
The Claranor UV decontamination tunnel is designed specifically for the surface decontamination of materials like large ingredient bags, plastic bins, and other packaging items. The system uses low pressure UV technology to achieve 360° surface coverage, ensuring that all areas of the material are thoroughly decontaminated before moving into high-care zones. The tunnel offers easy operation thanks to synchronisation with the production line.
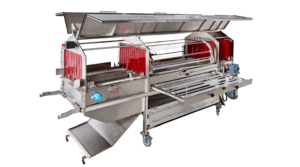
Key features and benefits of the Claranor decontamination tunnel
- Chemical-free solution
- Decontamination rate: >3 log reduction on E. coli or C. sakazakii on flat surfaces of the bag
- Maxi bag to be treated: 650m width, 900mm long and 350mm height
- Capacity: 120 bags/h Length (without inlet/outlet conveyor) : 2650mm Width : 1250mm
- Options: inlet/outlet conveyor, dedusting prior to treatment, panel screen/HMI on both sides
- UV dose monitoring
- Respects product integrity
- 360° Surface Coverage
- Fast and efficient: Materials pass through the tunnel quickly, allowing for continuous production with minimal downtime.
- User-friendly design: The Claranor tunnel is designed to be easy to operate, clean, and maintain.
- Adaptable and scalable: Claranor offers both standard and customized solutions to meet the specific needs of your production line. Whether you’re working with small packaging materials or large ingredient bags, the decontamination tunnel can be adapted to suit your requirements.
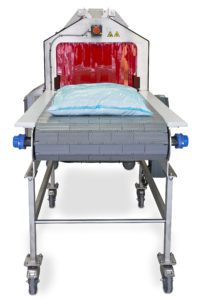
Comprehensive support services from Claranor
In addition to providing advanced decontamination equipment, Claranor offers a full suite of support services to ensure the success of your installation. From the initial design and engineering phase through to commissioning and maintenance, our team of experts is with you every step of the way.
• Microbiological validation: we provide microbiological validation to ensure that the system is achieving the required level of decontamination for your specific materials. This ensures that your production line meets the highest standards of hygiene and product safety.
• Commissioning and training: Once the system is installed, our team will work closely with your operators to ensure that they are fully trained on the equipment. We provide comprehensive training programs to ensure smooth operation and maximum efficiency.
• Preventive and corrective maintenance: To keep your system running at peak performance, Claranor offers preventive and corrective maintenance services. Our technicians are available to provide regular check-ups and address any issues that may arise, ensuring minimal downtime and maximum productivity.
For more information on our decontamination solutions
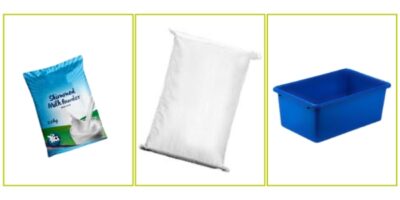