Packaging decontamination: chemical-free technologies take their place in the sun
UV-C, pulsed light, electron beams: these water- and chemical-free decontamination technologies are gradually finding their way into food processing plants.
Article published in RIA, November 25, 2024
Read original article
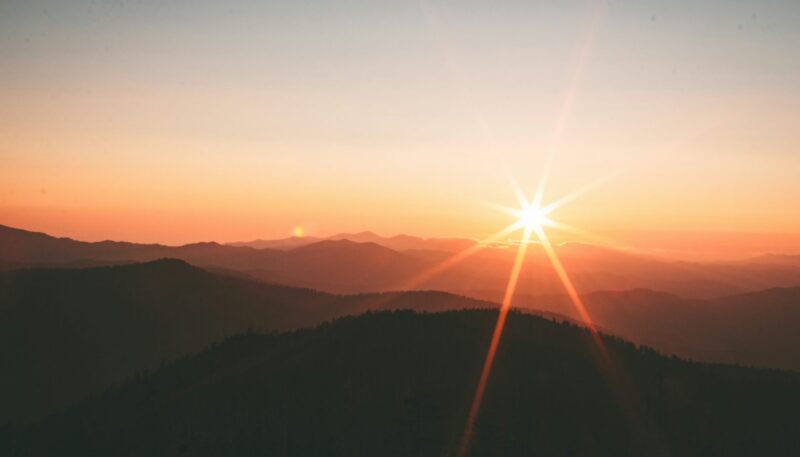
Chemical-free decontamination technologies
Technologies for safety and sustainability
For Christophe Riedel, Managing Director of Claranor and a pioneer in the field of pulsed light, the motivations of manufacturers are threefold: “Choosing a chemical-free technology is most often a question of safety and working conditions. Then there are economic and environmental motivations. Light-based decontamination processes consume less energy. What’s more, they don’t generate effluents, which are beginning to be taxed in some countries”.
Pulsed light, ultra-clean packaging reliable partner
The various technologies available on the market can handle all levels of decontamination, from the most basic to aseptic. Pulsed light is particularly well positioned for intermediate levels: “We generally respond to requests for ultra-clean packaging, which corresponds to VDMA* hygiene class IV. Products requiring this level of hygiene are typically microbiologically unstable, sold in refrigerated circuits, with a pH above 4.6, or with a long shelf-life. These include plant-based milks and desserts, and beverages such as kombucha. Ultra-clean packaging may also be required in the manufacture of sauces, when products contain no preservatives or are pasteurized and then filled cold”, explains Christophe Riedel.
Residue-free chemical solutions for every package
For all these applications using light, the technical challenge is to be able to expose the entire surface of the packaging, for a sufficiently long time to kill the micro-organisms. The nature and shape of the packaging, as well as the production rate, are criteria which will guide the choice of one technology over another, as will the expected level of decontamination. On the whole, film decontamination prior to package forming is a very successful application. Light is also used to achieve reductions of up to 3 logs on caps and necks of high-speed preforms, and more recently on preformed cups and metal cans.
Claranor: proven, recognized expertise
One of the driving forces behind the adoption of chemical-free decontamination is the very positive feedback received, notably the disappearance of contamination after the installation of pulsed light equipment. These references are the most talked-about within the groups, and bear witness to the effectiveness of these systems. Then there’s the industrial guarantee, a feedback from users who have operated equipment over long periods. Reliability and the quality of customer service are also decisive factors. “Today, we have 15 years’ experience of pulsed light worldwide, and this technology has been used for 10 years by Danone in the United States. This is reassuring for all players wishing to get started”, concludes Christophe Riedel.